El INTI está desarrollando un equipo para fortalecer las capacidades del sistema sanitario ante la pandemia del COVID-19, junto con un consorcio de pymes industriales y otros organismos públicos. Además, el instituto está colaborando con más de 10 proyectos de respiradores en todo el país y otras iniciativas relacionadas con la emergencia sanitaria.
A máxima velocidad, como pasa con las soluciones médicas pensadas para cubrir necesidades en tiempos de pandemia, en menos de dos meses de trabajo, un consorcio que integró el trabajo de cincuenta investigadores estatales y de especialistas de empresas privadas logró poner a punto la primera partida de “respiradores alternativos”, que pueden usarse con pacientes de Covid-19 en salas de cuidados intermedios, o -provisoriamente- en una terapia intensiva.
“Tomamos una idea originalmente desarrollada en el Massachussets Institute of Technology (MIT) la adaptamos y la mejoramos de manera de poder hacer un producto más confiable, durable y que -además- pueda ser fabricada por empresas nacionales, con insumos locales”, explicó el ingeniero Claudio Berterreix, director del Centro de Mécanica del Instituto Nacional de Tecnología Industrial (Inti).
El desarrollo consiste en la automatización de una bolsa de ventilación manual -denominada AMBU (Airway Mask Bag Unit)- que durante una emergencia médica se usa en forma manual para dar apoyo respiratorio en forma transitoria. El equipo en cuestión es simple y puede ser utilizado por un paciente por hasta 48 horas seguidas, una cantidad de tiempo menor a la que permiten los respiradores de alta tecnología. Pero su función no es reemplazarlos sino que los terapistas dispongan de respiradores complementarios a los que recurrir ante un desborde de casos, durante un eventual pico de la pandemia. Además de cumplir con su función mecánica, el ventilador del Inti está equipado, además, con un sistema de filtros que se ubican entre el tubo intratraqueal y el dispositivo para que el aire exhalado por el paciente no esté contaminado por el coronavirus.
En los ensayos realizados en las últimas semanas, el prototipo del equipo superó las prestaciones mínimas de eficacia que exigen los expertos de la Asociación de Anestesia Analgesia y Reanimación de Buenos Aires.
“Armamos un equipo de más de cincuenta expertos para poder avanzar rápido, sumando tecnólogos del Instituto de Investigaciones Científicas y Técnicas de Defensa, de Fabricaciones Militares, de la facultad de ingeniería del Ejército y desarrolladores de un grupo de Pymes dedicadas a la fabricación mecánica y de insumos de equipamiento de salud. Entre todos, en tiempo récord, perfeccionamos el modelo y fabricamos cinco equipos de preserie para poder comenzar con la homologación oficial del producto”, detalló Berterreix.

“EN LAS PRÓXIMAS DOS SEMANAS ESPERAMOS TENER LISTO EL DISPOSITIVO FINAL”
Justamente, Rubén Geneyro, presidente del INTI informó que “ya estamos en la instancia final de los ensayos de eficacia y seguridad que requieren todos los equipamientos médicos. En las próximas dos semanas esperamos tener listo el dispositivo final y toda la documentación que requiere Anmat”.
El desarrollo local -del que eventualmente se podría llegar a fabricar hasta 250 unidades diarias- se logró con un financiamiento mixto que sumó dinero de la Agencia de Promoción de Investigación y Desarrollo, aportó unos $12 millones, a los que se sumaron $ 7,6 millones de inversión privada. Aunque el costo final de estos respiradores dependerá de la cantidad que se fabrique y de la disponibilidad de los insumos, los estudios iniciales marcaban que podría rondar los US$ 500 por unidad.
Aumento de producción
El desarrollo del INTI que suma un nuevo tipo de equipo médico para restar gravedad al déficit argentino en materia de respiradores, se le suma otro aporte que llega desde el sur: a partir de fines de mayo una firma de Tierra del Fuego, usualmente enfocada en el mercado de la electrónica instaló una línea de montaje para la fabricación de respiradores mecánicos. Se trata de Mirgor que firmó un acuerdo con Leistung -la Pyme cordobesa especializada en insumos de salud que ya fabricaba estos equipos- pero que tenía su capacidad de producción totalmente saturada. Según fuentes de Mirgor, Leistung tenía una capacidad de entrega de hasta 50 aparatos mensuales. Ahora, tras la alianza, podrán llegar a fabricar hasta 1000 dispositivos mensuales.
Por otra parte, en marzo pasado varias automotrices argentinas comenzaron a trabajar en este tipo de proyectos. Y esta semana VW Argentina se convirtió en la primera en entregar algo de este tipo. Se trata de un dispositivo de ventilación mecánica no invasiva, diseñado y fabricado por los ingenieros de mantenimiento de la planta de transmisiones de VW en Córdoba. Y fue donado a la municipalidad de la capital de esa provincia. No se conocieron los detalles técnicos pero se trata de un dispositivo centralizado que -según publicó en sus redes Thomas Owsianski, CEO de VW Argentina, “lo fabricaron bajo el asesoramiento de la doctora Perla Pahnke, Jefa de Emergentología, y de Cristina Gómez, Jefa de Terapia en el Hospital Municipal de Urgencias”. Y sirve para abastecer de oxígeno a hasta 20 pacientes en forma simultánea”.
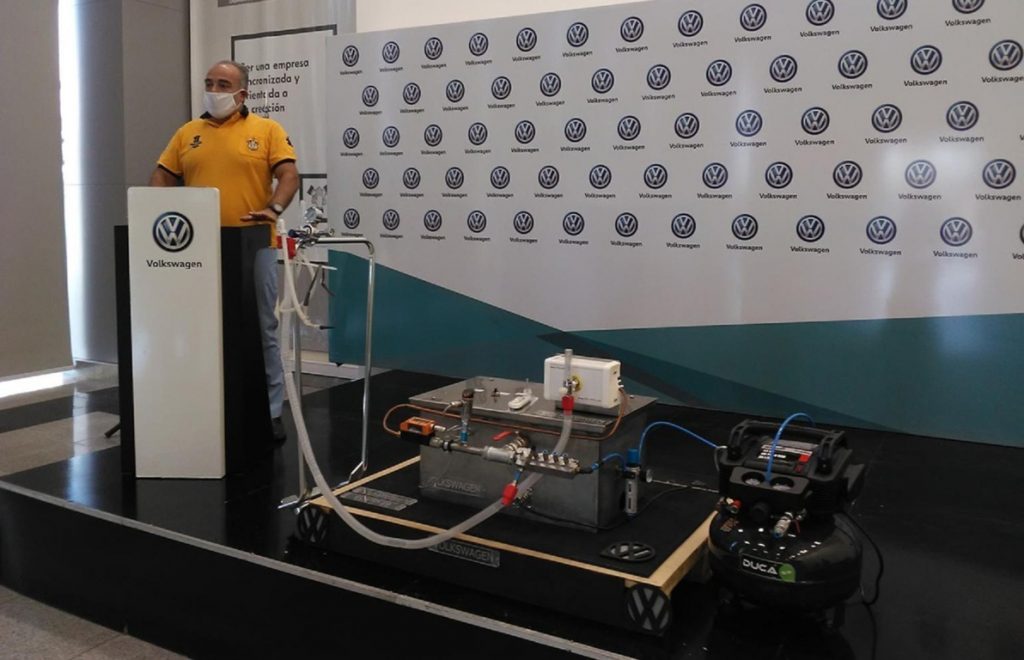